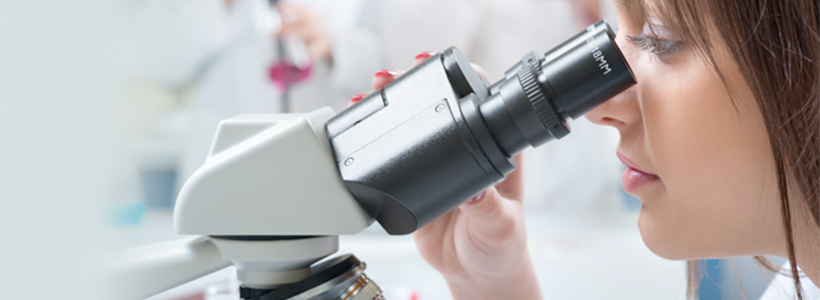
The research work was mainly focused on the design and characterization of gastro retentive Abacavir floating microballoons as to retain the formulation for a prolonged period of time and deliver the drug to the site of absorption. This work focused on to investigate the suitability of different viscosities of ethyl cellulose in different concentrations. Abacavir Sulphate is a recently approved anti-retro-viral drug with very short biological half-life (1.0 hrs) and bioavailability (70%), it has better absorption from upper part of GIT. The microballoons were prepared by non-aqueous solvent evaporation method using polymer such as different concentrations of Hydroxy Propyl Methyl Cellulose ethyl cellulose, in different ratios and Abacavir Sulphate in each formulation. The prepared microballoons were characterized by polymer compatibility (FTIR), The FTIR spectra of drug and different polymers showed no shift in peak, hence no interaction. Micromeritic properties such as Bulk density, Tapped density, Carr’s index and Angle of repose. Other properties including percentage of floating buoyancy, drug entrapment efficiency, percentage of yield, in vitro drug release and SEM studies. The yield of the formulated floating microballoons was in the good range. The results of drug entrapment efficiency were in the range of 67 + 2.23 to 98.9 + 2.51%, as the core to coat ratio increased there was an increase in entrapment efficiency. The percentage of floating buoyancy was found that in the range of 70.2+ 3.01 % to 81+ 2.81% and the floating microballoons had no floating lag time. Scanning electron microscopy (SEM) confirmed their spherical size, perforated smooth surface and a hollow cavity in them. The best drug release, entrapment efficiency and percentage of floating buoyancy profiles were seen with formulation AS10 at the ratio of drug to polymer (EC) of 1:5.